Mục lục
ToggleIntroduction to Precision Machining for Engine & Transmission Systems
What is Precision Machining?
Precision machining refers to the process of removing material from a workpiece to create highly accurate components with tight tolerances. This is achieved using advanced CNC (Computer Numerical Control) machines, which ensure high levels of precision and repeatability.
In industries such as automotive and aerospace, precision machining is crucial for producing components that meet strict quality and performance requirements. The ability to manufacture complex parts with micron-level accuracy makes this technology indispensable in modern manufacturing.
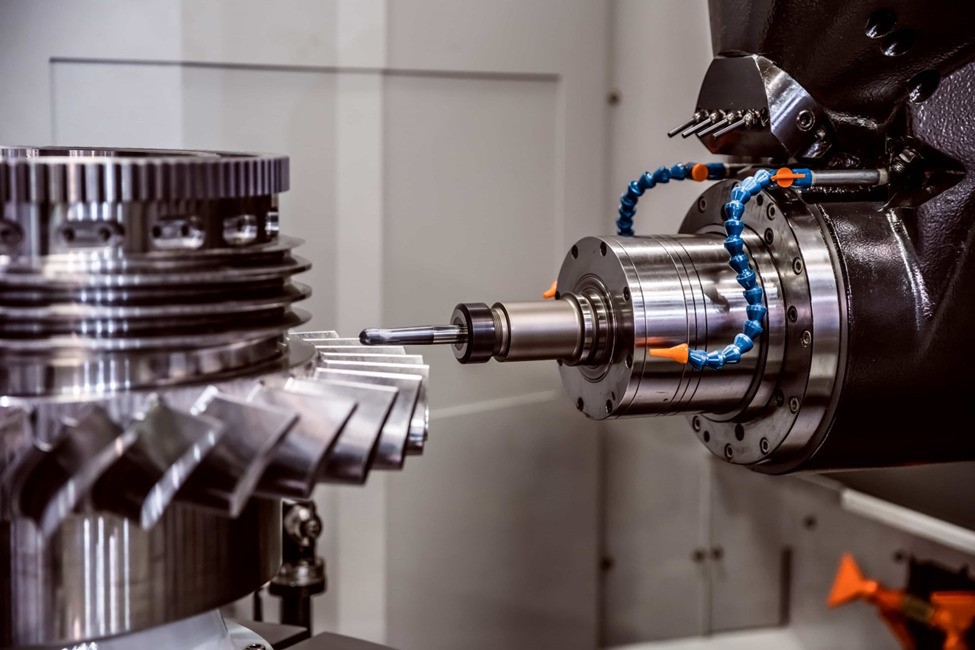
Why Precision Machining Matters in Engine & Transmission Manufacturing
Precision machining plays a critical role in producing high-performance engine and transmission components. Here’s why:
- Ensures tight tolerances & durability – Precision-machined parts fit seamlessly, reducing wear and tear over time.
- Enhances performance & efficiency – Optimized components improve fuel efficiency and power delivery.
- Reduces mechanical failures – High-precision parts minimize friction, heat buildup, and structural weaknesses.
Precision Machining Components in Engine & Transmission Systems
Critical Engine Components Manufactured with Precision Machining
Modern engines require high-precision parts to function efficiently. Some of the most critical engine components manufactured using precision machining include:
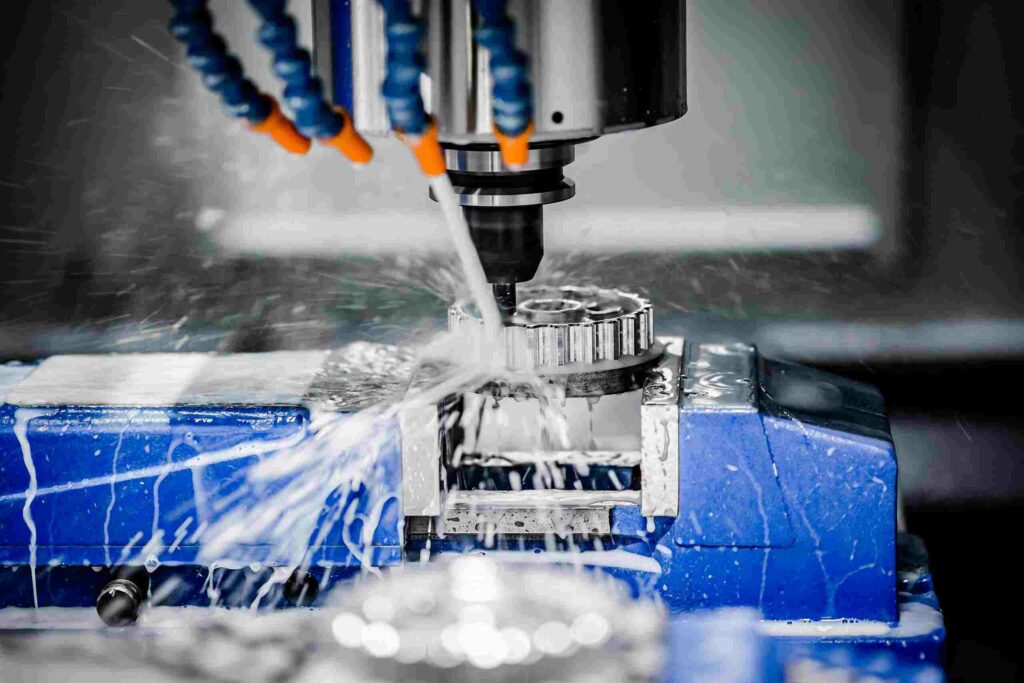
- Cylinder Heads – Houses intake and exhaust valves, requiring precise machining for proper sealing and airflow.
- Pistons & Connecting Rods – Must be lightweight yet durable to withstand high pressures and temperatures.
- Crankshafts & Camshafts – Essential for converting linear motion into rotational motion, requiring extremely tight tolerances.
- Engine Blocks – The foundation of an engine, where every bore and thread must be machined with extreme accuracy.
Precision Machining in Transmission Systems
Transmission components are equally dependent on precision machining for smooth and efficient power transfer. Key machined parts include:
- Gears & Gear Shafts – Require high-precision cutting and grinding for seamless engagement and minimal friction.
- Transmission Casings – Machined for structural integrity and proper alignment of internal components.
- Synchronizers & Clutch Components – Ensure smooth shifting and power transmission with minimal wear.
- Bearings & Housings – Machined for tight tolerances to reduce friction and maximize lifespan.
Benefits of Precision Machining for Automotive & Industrial Applications
Superior Accuracy & Consistency: Precision machining guarantees that engine and transmission components are manufactured with repeatable accuracy, ensuring optimal performance and longevity.
Enhanced Material Strength: Machined components undergo rigorous material selection and finishing processes to withstand extreme conditions such as high temperatures and pressures.
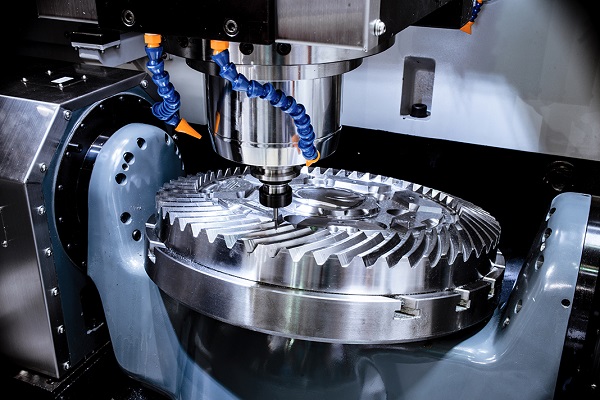
Increased Efficiency & Fuel Economy: By reducing friction and improving gear alignment, precision machining helps enhance engine and transmission efficiency, contributing to better fuel economy and performance.
Cost-Effective Production: CNC precision machining minimizes material waste and human error, leading to reduced production costs and higher overall efficiency.
CNC Machining Technologies Used in Precision Manufacturing
Precision machining relies on advanced CNC technologies to achieve high accuracy, consistency, and efficiency in manufacturing engine and transmission components. Various machining techniques, such as milling, turning, grinding, and quality control processes, ensure that each part meets the stringent requirements of the automotive and industrial sectors.
CNC Milling & Turning
CNC milling and turning are fundamental processes in precision machining, enabling the production of highly complex and intricate components. These methods provide exceptional precision, reduce material waste, and improve production efficiency, making them ideal for manufacturing critical engine and transmission parts.
- 5-axis CNC machining – Used for manufacturing complex engine components like cylinder heads and camshafts.
- High-speed turning – Ideal for producing shafts, gears, and other rotational components.
Grinding & Surface Finishing
Grinding and surface finishing are essential for achieving the required smoothness, accuracy, and durability of machined components. These processes help refine surfaces to meet strict performance standards, reduce friction, and enhance resistance to wear and corrosion.

- High-precision grinding – Achieves micron-level tolerances for optimal performance.
- Polishing & coating – Enhances durability by reducing corrosion and wear.
Quality Control & Inspection
To maintain the highest level of precision, stringent quality control and inspection measures are integrated into the manufacturing process. These techniques help detect defects early, ensure compliance with design specifications, and enhance overall production efficiency.
- CMM (Coordinate Measuring Machine) inspection – Ensures all parts meet design specifications with extreme accuracy.
- Real-time production monitoring – Helps maintain zero-defect manufacturing through continuous quality checks.
Applications of Precision Machining in Various Industries
Automotive Industry
- Engine blocks, crankshafts, pistons – Require high-precision machining for durability and performance.
- Gear systems & turbochargers – Precision components that improve power delivery and efficiency.
Aerospace Industry
- Jet engine components – Demands extremely tight tolerances for optimal flight performance.
- Landing gear parts – Must be lightweight yet durable to handle extreme stress.
Industrial Machinery: Heavy-duty gears & hydraulic systems – Require precise machining to ensure longevity and efficiency.
Medical Devices: Precision surgical instruments & implants – High-accuracy machining ensures safety and effectiveness in medical applications.
Conclusion – The Future of Precision Machining in Engine & Transmission Systems
With advancements in AI and automation, precision machining continues to evolve, enabling even greater levels of accuracy and efficiency. Future trends include:
- Smart machining with AI-powered real-time monitoring – Enhances quality control and reduces defects.
- Sustainable machining solutions – Focuses on reducing material waste and energy consumption.
- Growing demand for EV & hybrid vehicle transmission systems – Precision machining will play a vital role in producing lightweight, high-efficiency components for next-generation vehicles.
As industries continue to push for higher performance and sustainability, precision machining remains the backbone of modern engine and transmission manufacturing. Businesses looking to stay ahead must invest in high-quality CNC machining technologies to meet evolving market demands.