Mục lục
Toggle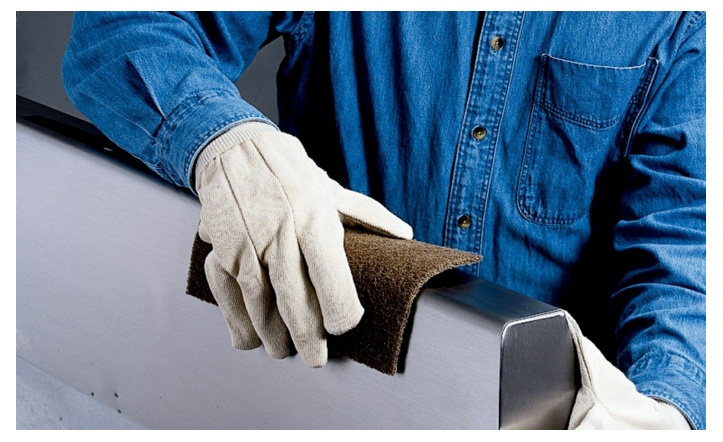
Introduction to metal surface treatment and coating
What is metal surface treatment?
Metal surface treatment is a crucial industrial process that enhances the durability, corrosion resistance, and overall performance of metal components. It involves various techniques that modify the physical, chemical, and mechanical properties of the metal surface, ensuring optimal functionality for different applications.
This process is widely used in automotive, aerospace, construction, medical, and heavy machinery industries to increase metal longevity, improve aesthetic quality, and prepare surfaces for better adhesion of coatings and paints.
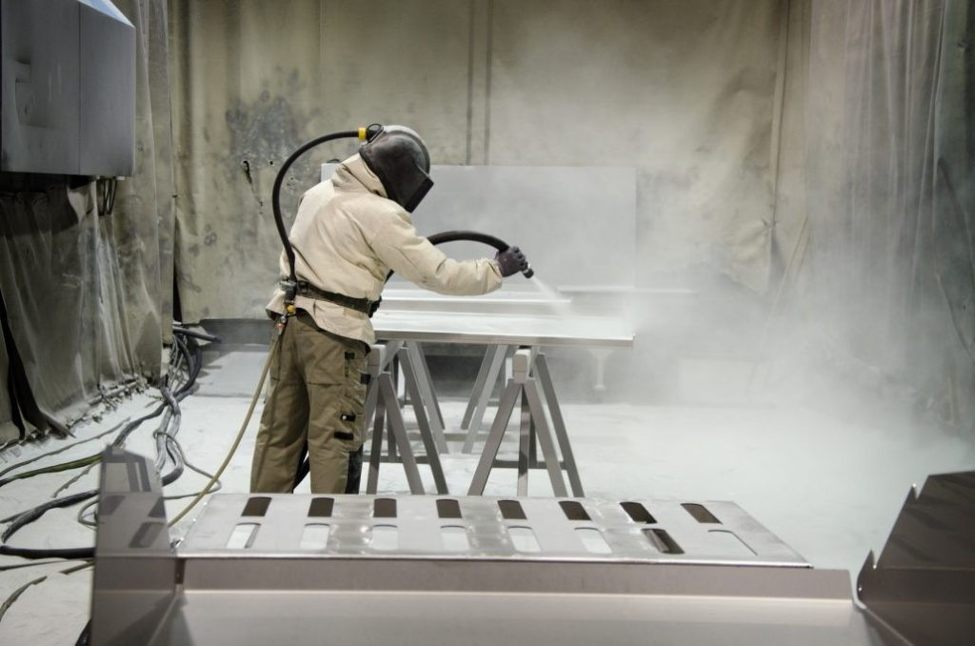
Why is surface treatment crucial for industrial applications?
Surface treatment is essential for industrial applications due to the following benefits:
- Prevents oxidation, rust, and wear – Protects metals from environmental damage, especially in harsh conditions.
- Improves adhesion for coatings & paints – Ensures better bonding for protective and decorative layers.
- Enhances electrical conductivity and heat resistance – Optimizes performance in electronics, aerospace, and energy sectors.
In 2025, advancements in automation, eco-friendly solutions, and nano-coating technologies are transforming metal treatment processes, making them more efficient and sustainable.
Common metal surface treatment methods in 2025
With technological advancements, metal surface treatment and coating methods are evolving to provide stronger, longer-lasting, and more environmentally friendly solutions. Below are the most effective metal treatment techniques used in 2025.
Mechanical surface treatment
Mechanical processes involve abrasive and surface-modifying techniques to improve metal properties.
- Sandblasting & Shot Peening – Removes contaminants, improves fatigue strength, and enhances surface roughness for better paint and coating adhesion.
- Grinding & Polishing – Creates smooth, mirror-like finishes, reducing friction and enhancing wear resistance. Common in medical implants and precision machinery.
- Laser Surface Texturing – Uses high-precision laser beams to create micron-level surface textures, improving lubrication retention, adhesion, and corrosion resistance.
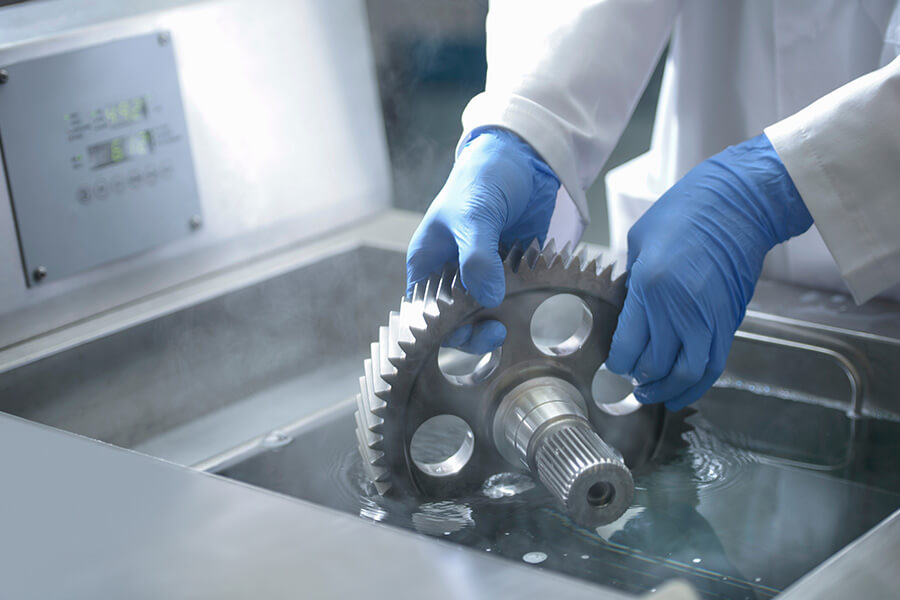
Thermal surface treatment
Heat-based treatments improve metal hardness, toughness, and wear resistance.
- Heat Treatment (Tempering, Annealing, Nitriding) – Increases metal durability, flexibility, and fatigue resistance, essential for automotive and aerospace components.
- Plasma Nitriding & Carburizing – Surface hardening processes that increase wear and corrosion resistance, widely used for gears, shafts, and tooling equipment.
- Hot-Dip Galvanizing – Zinc coating process that protects steel structures, automotive parts, and outdoor metal applications from corrosion.
Electrochemical surface treatment
Electrochemical processes alter the chemical properties of the metal surface to improve corrosion resistance, durability, and aesthetics.
- Anodizing – Common for aluminum, this process enhances wear resistance, corrosion protection, and surface hardness.
- Electroplating (Nickel, Chrome, Zinc, Gold) – Creates decorative and protective layers, widely used in electronics, automotive parts, and jewelry manufacturing.
- Lắng đọng điện di (E-Coating) – Một kỹ thuật phủ đồng nhất, thân thiện với môi trường, mang lại khả năng bảo vệ chống ăn mòn tuyệt vời cho các bộ phận ô tô và công nghiệp.
Read more: Precision Machining for Engine & Transmission Systems – High-Quality CNC Components
Advanced coating technologies
Innovative coating solutions are revolutionizing metal protection and performance.
- Powder Coating – Eco-friendly, solvent-free alternative to liquid paint, offering superior durability and scratch resistance.
- Ceramic & Thermal Spray Coatings – Used in high-temperature environments such as aerospace, turbine engines, and industrial machinery.
- PVD (Physical Vapor Deposition) Coatings – Ultra-thin, hard coatings applied to cutting tools, aerospace components, and luxury goods for superior wear resistance.
Choosing the right metal treatment process
Selecting the optimal metal surface treatment method depends on industry requirements, material properties, and cost factors.
Application-specific needs
Each industry demands specific surface treatments for optimal performance:
- Automotive – Galvanizing, powder coating, and electroplating for corrosion protection.
- Aerospace – PVD coatings, anodizing, and thermal spray coatings for high-temperature resistance.
- Medical – Electropolishing, anodizing, and plasma nitriding for sterilization and biocompatibility.
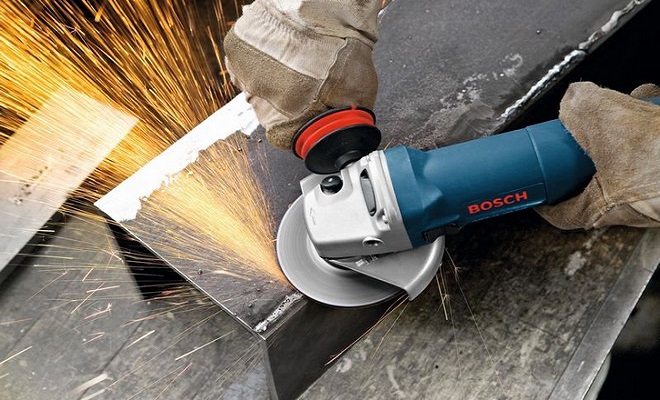
Material compatibility
Not all treatments are suitable for all metals. Choosing the right method depends on:
- Stainless Steel – Electropolishing, passivation, and nitriding.
- Aluminum – Anodizing and powder coating for improved corrosion resistance.
- Titanium – PVD coatings and anodizing for enhanced strength and aesthetics.
- Carbon Steel – Galvanizing, carburizing, and electroplating to prevent rust.
Cost versus durability
Manufacturers must balance cost-effectiveness and long-term durability:
- Low-cost solutions – Powder coating, electroplating, and galvanizing for basic protection.
- High-performance coatings – PVD, plasma nitriding, and ceramic coatings for superior wear resistance.
Future trends in metal surface treatment
The metal treatment industry is advancing towards automation, sustainability, and high-performance coatings. Key trends in 2025 include:
Automation & AI-Powered coating systems
AI-driven robotic coating systems improve:
- Precision and efficiency in powder coating, PVD, and anodizing.
- Reduced material waste and improved process consistency.
Eco-friendly and non-toxic surface treatments
Global regulations are pushing manufacturers towards sustainable treatments:
- Water-based coatings to replace solvent-based solutions.
- Chemical-free anodizing and powder coating to reduce environmental impact.
Nano-coatings for high-performance applications
Nano-technology is revolutionizing metal protection with:
- Self-healing coatings that repair minor scratches automatically.
- Anti-bacterial coatings for medical and food processing industries.
- Superhydrophobic coatings to prevent water and corrosion damage.
Conclusion
Metal surface treatment and coating technologies are essential for enhancing the durability, functionality, and aesthetic quality of metal components. As automation, eco-friendly processes, and nano-coatings continue to evolve, staying ahead of new metal treatment technologies ensures businesses remain innovative, cost-effective, and compliant with global standards.